Best Practices for Preventing Weld Undercut: Mastering the Basics
Best Practices for Preventing Weld Undercut: Mastering the Basics
Blog Article
Understanding the Art of Welding: Exactly How to Stay Clear Of Undercut Welding Issues for Flawless Construction Outcomes
By comprehending the origin creates of undercut welding and applying effective techniques to avoid it, welders can raise their craft to brand-new degrees of quality. In the search of remarkable manufacture outcomes, understanding the art of welding to avoid undercut issues is not just a skill but a necessity for those striving for perfection in their work.
Understanding Undercut Welding
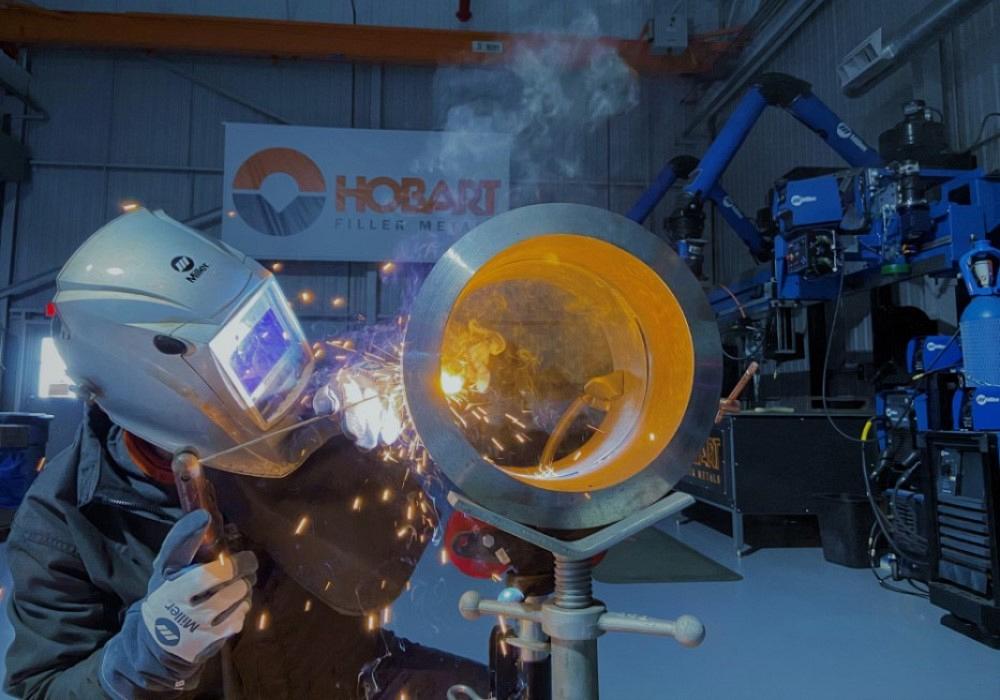
To avoid undercut welding, welders must make sure correct welding criteria, such as readjusting the existing, voltage, traveling rate, and keeping the proper electrode angle. By recognizing the reasons of undercut welding and applying preventative actions, welders can achieve top quality, structurally audio welds.
Sources Of Undercut in Welding
Comprehending the variables that contribute to undercut in welding is crucial for welders to create high-grade, structurally sound welds. Insufficient welding incorrect or current welding rate can additionally contribute to undercut. Comprehending these reasons and executing appropriate welding strategies can help stop damaging issues, guaranteeing resilient and strong welds.
Strategies to stop Undercutting

To alleviate the danger of damaging in welding, welders can utilize tactical welding techniques aimed at boosting the top quality and honesty of the weld joints. Furthermore, utilizing the appropriate welding technique for the specific joint configuration, such as weave or stringer grains, can add to decreasing undercutting.
Utilizing back-step welding strategies and managing the weld grain profile can likewise aid distribute warmth evenly and lessen the threat of undercut. Routine examination of the weld joint during and after welding, as well as carrying out quality assurance actions, can aid in finding and addressing undercutting problems without delay.
Importance of Appropriate Welding Criteria
Picking and maintaining suitable welding criteria is important for attaining successful welds with very little flaws. Welding criteria describe variables such as voltage, current, travel speed, electrode angle, and protecting gas circulation price that straight influence the welding process. These parameters should be very carefully readjusted based upon the kind of product being bonded, its thickness, and the welding technique employed.
Proper welding parameters guarantee the correct amount of warm is used to thaw the base steels and filler product evenly. If the criteria are established also high, it can bring about excessive heat input, causing distortion, burn-through, or spatter. On the other hand, if the criteria are also reduced, insufficient that site combination, lack of penetration, or undercutting might take place.
Quality Assurance in Welding Operations
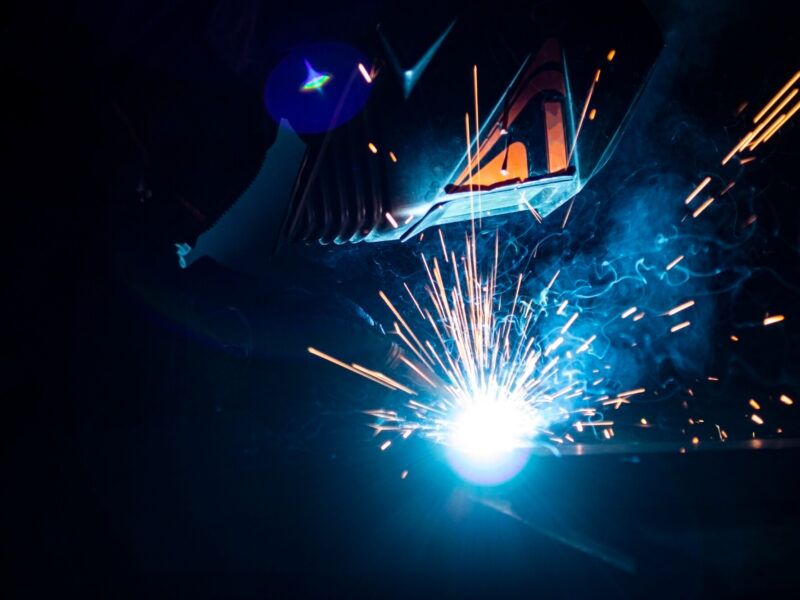
Verdict
Finally, grasping the art of welding needs a thorough understanding of undercut welding, its reasons, and techniques to avoid it. By ensuring proper welding specifications and applying quality guarantee techniques, flawless construction results can be achieved. It is essential for welders to continually make every effort for excellence in their welding operations to avoid undercut concerns and generate premium welds.
Undercut visit this web-site welding, an usual problem in welding processes, occurs when the weld steel doesn't correctly load the over at this website groove and leaves a groove or anxiety along the welded joint.To prevent undercut welding, welders ought to guarantee proper welding criteria, such as readjusting the current, voltage, travel speed, and keeping the correct electrode angle. Poor welding existing or wrong welding speed can additionally add to damage.To reduce the risk of damaging in welding, welders can utilize strategic welding techniques intended at improving the quality and stability of the weld joints.In final thought, mastering the art of welding needs an extensive understanding of undercut welding, its reasons, and methods to stop it.
Report this page